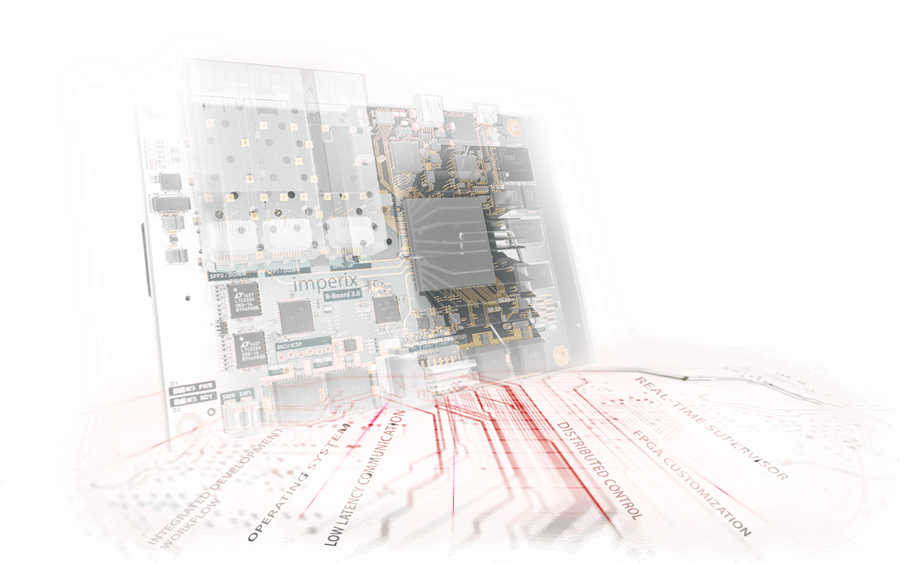
Networked control technology
Modular control solutions for power electronics
Our proprietary networked control technology is at the heart of our fully programmable control systems.
This brings very high flexibility to our digital controllers, enabling them to control all sorts of power converters, ranging from conventional inverters to more complex modular, or multilevel power converters.
Networked control technology
Distributed converter control made simple
Various master-slave arrangements
All control devices can be operated as if they belonged to a single larger controller. Only one CPU is operated, with possibly multiple FPGAs.
Multiple control loops can be operated within multiple CPUs, possibly at different rates. Networked control devices require independent control software.
Benefits of the RealSync technology
Imperix’s networked control technology supports various types of data exchanges between power converter controllers.
Fast local control loops
Fast closed control loops can be easily implemented within local controllers.
Fast global control loops
Networked control systems can also implement fast global control loops, thanks to the very low latency of the communication.
Fast inter-devices communication
Communication between the different controllers (hierarchized or not) can also benefit from very fast data transfers.
Accurate network-level synchronization
Once interconnected, all devices benefit from a common time base, serving as a global reference for precise timing management.
High-speed serial interconnect
Ultra-low latency communication protocol
Getting the most from the network topology
The imperix RealSync protocol exploits the particular characteristics of the networked control traffic in order to reduce latency. Notably, for the relatively small payloads involved, it turns out that tree-shaped network topologies offer a superior usage of the total available bandwidth.
Data traffic (3000 nodes) | 1-tree | 2-tree | Gain |
---|---|---|---|
DTOT with 64 Bytes | 557 µs | 357 µs | x 1.5 |
DTOT with 16 Bytes | 554 µs | 119 µs | x 4.7 |
The table shows the total data transfer delay DTOT for different values of payload size, as a function of the networked control topology. It appears that a pyramidal structure offers almost 5x superior performance versus the conventional ring-type networks.
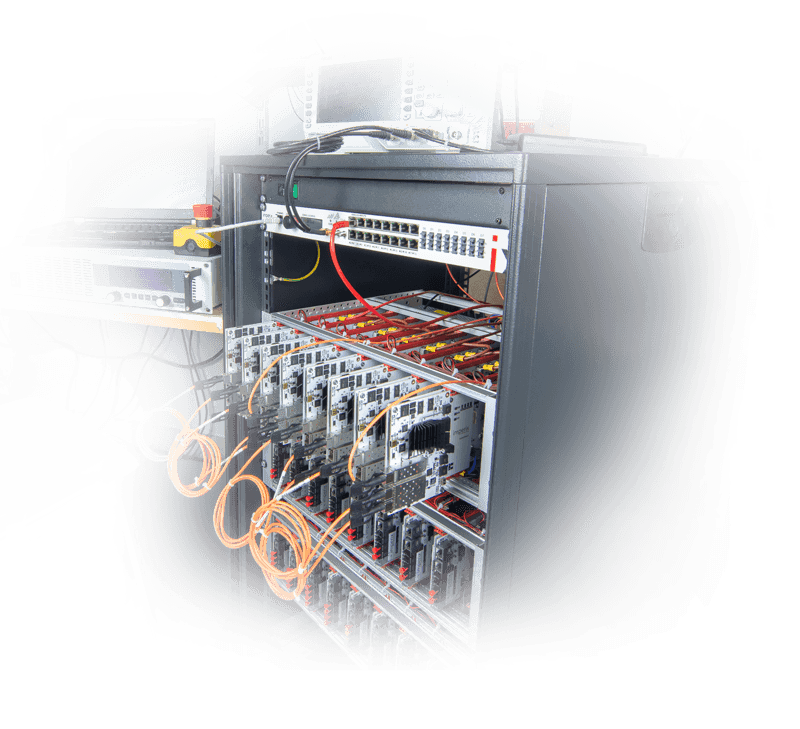
Synchronization Technology
Distributed modulation for power converters
Clock dissemination over SFP+
Networked control requires that all devices are precisely synchronized. Indeed, this is essential so that all PWM channels behave consistently, or that all measurements are taken at the exact same time.
This is why RealSync ensures the proper synchronization of all connected devices, down to an accuracy of only ±2ns.
Transparent operation of interleaved converters
Thanks to their native synchronization, imperix converter controllers implement pulse-width modulation (PWM) in a fully distributed fashion.
Indeed, modulators are located directly inside the slaves, hence facilitating modular networked control implementations, but without impeding the timing accuracy.
Networked control implementation
FPGA-based control
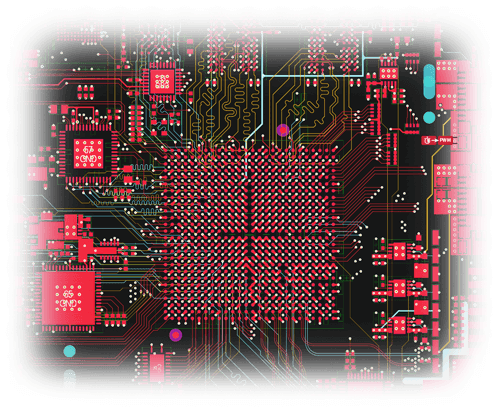
Getting the most from distributed control
Our modular control systems rely heavily on FPGA devices for communication, signal processing and distributed modulation. That said, numerous distributed control strategies also require FPGAs.
In this context, imperix offers to its customers to edit both the CPU software – supporting automated code generation – as well as FPGA firmware. Development engineers can therefore also disseminate their own algorithms among the control network.
Imperix controllers support a broad range of programming frameworks
Engineers can add custom-designed FPGA firmware to all imperix controllers. To this end, the most common development environments and tools are supported, including Xilinx Vivado HLS, Xilinx System Generator, Matlab HDL Coder, and of course manual VHDL code edition.
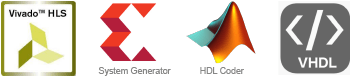
Dedicated operating system
Network and hardware abstraction
Implementing modular control systems may seem uneasy, especially over a network. For this reason, our operating system takes care of everything!
In the end, users can focus exclusively on control design, rather than overcoming other technical challenges. Notably, interrupts, faults management, monitoring and other similar tasks are handled transparently. This means that the underlying hardware and network aren’t visible to the users. All they see is an easy-to-use modular control system.
BBOS operating system
It contains application-specific control algorithms. It is developed by the end-user using C/C++, Simulink or PLECS functions that are always kept unchanged, independently of the underlying hardware.
This is the essence of the BBOS operating system. It makes sure that the desired configuration is valid (possibly across the control network) and guarantees the safe and sound execution of the control at the desired interrupt period.
It is the interface between immutable user-level functions and the always-evolving underlying hardware. Thanks to this layer, imperix controllers can be guaranteed to always be able to run existing software, even on future equipment.
Three products, one software
All programmable controllers with SFP connectivity are compatible with networked control. They also benefit from the same software development environment. As such, they can be mixed inside the same control network, or can be substituted for each other as a function of the technical requirements.

- DSP+FPGA
- 16x ADC channels
- Programmable analog front-end
- Hardware protections
- Excellent EMC
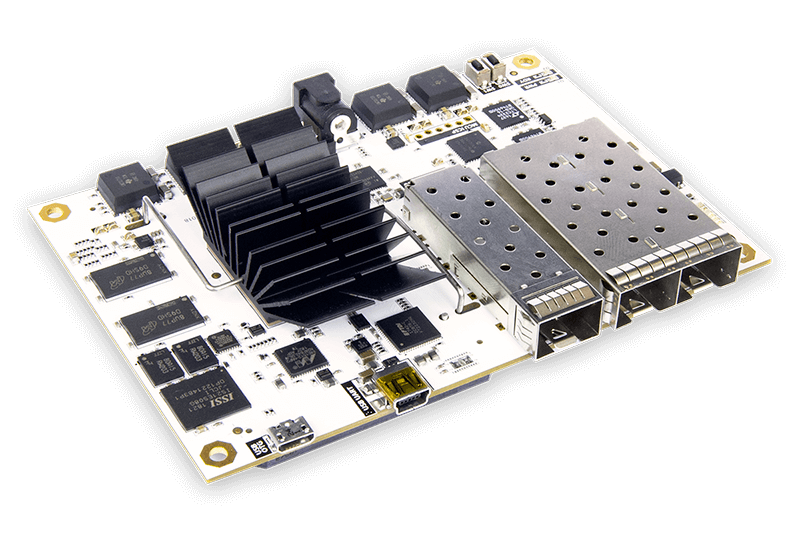
- DSP+FPGA
- 8x ADC channels
- 100% compatible with B-Box RCP
- Product-embeddable

- FPGA only
- 6x ADC channels
- Lowest cost
Computer-based software
Fully-Integrated development workflow
Our digital controllers benefit from the same control technology, software development environments, and performance characteristics. Therefore, they can be mixed inside the same control network, or can be substituted for each other as a function of the technical requirements.
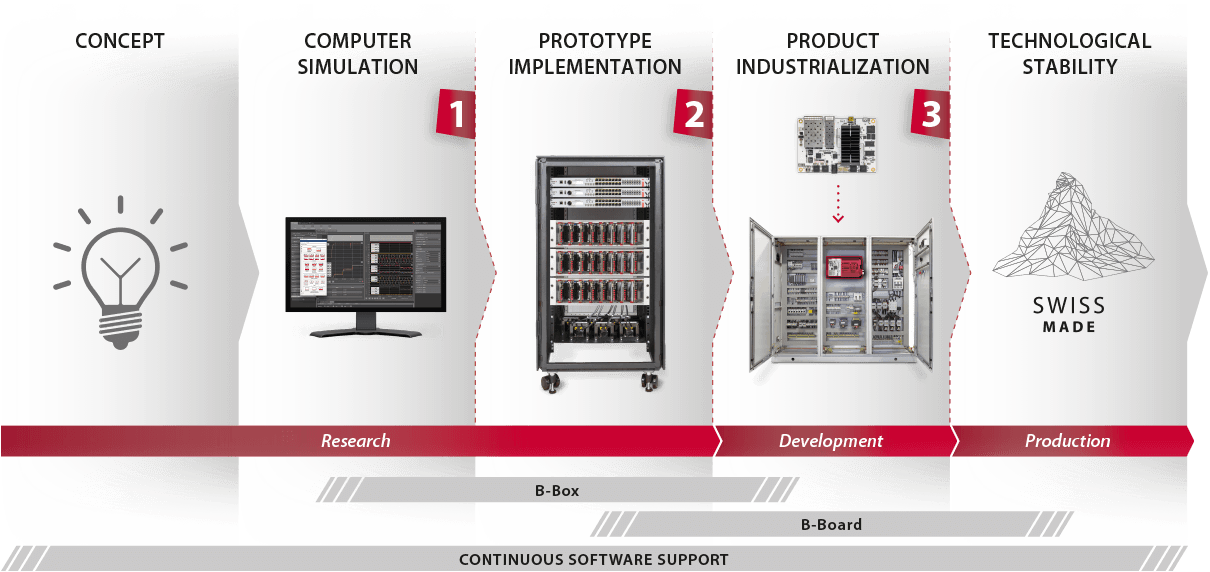

From the computer to the laboratory
First, engineers can switch swiftly from computer-based simulation to prototype implementation, thanks to automated code generation tools.

From the laboratory to the field
Then, the usual re-start that occurs when moving from prototyping equipment to series hardware can be alleviated by directly using B-Board PRO for final products.

From prototypes to mature products
Finally, imperix customers always benefit from an always up-to-date equipment, which guarantees operation over the long run, independently of the hardware evolution.