Key specifications
- Three-phase two-level
- LC and EMC filters
- AC precharge circuit
- V/I sensors
- B-Board PRO controller
- Up to 800 VDC
- Up to 32 A (RMS) at 50 kHz
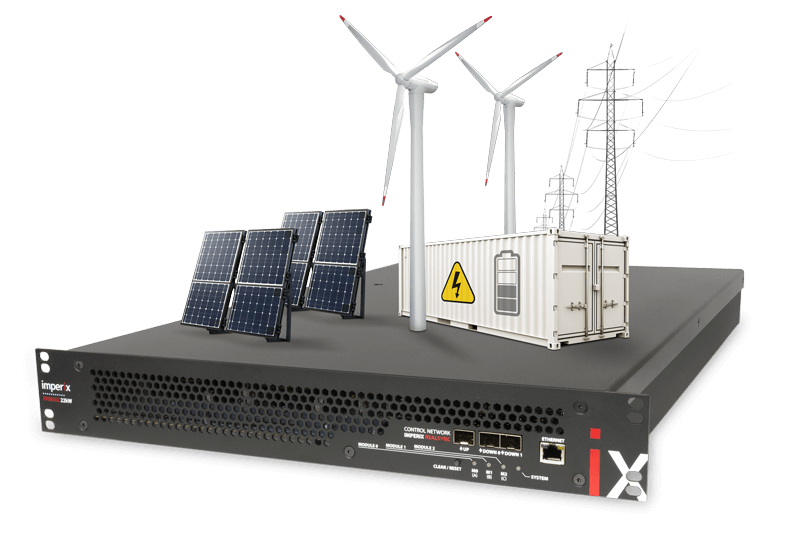
Programmable inverter
TPI8032 22kW
Unlike off-the-shelf industrial inverters, the TPI is fully programmable and allows the implementation of the most advanced control techniques on both its DSP and FPGA.
Thanks to its ultra-fast switching Silicon Carbide MOSFETs and its high-performance controller, the programmable inverter can notably be used for medium-frequency, hard-switched applications up to 150 kHz.
The all-in-one solution for microgrid applications
![]() | |
your price | |
What is included in the programmable inverter?
Control and power combined into a compact system

LC and EMC filters
A comprehensive filtering solution ensures excellent power quality, with quasi-sinusoidal output voltages and currents. As a result, the programmable inverter complies with the CISPR11 EMC standard.
Automated AC precharge circuit
The precharge procedure of the DC bus is fully automated and prevents the uncontrollable flow of currents through the anti-parallel body diodes of the MOSFETs. It enables safe and seamless connection to the grid.
Safe Operating Area (SOA) protections
SOA protections safely deactivate the power stage in case of hazardous behavior. They prevent the system from exceeding its rating during normal conditions and protect it against fast transient phenomenons (e.g. over-current/voltage).
TYPICAL APPLICATIONS OF THE PROGRAMMABLE INVERTER
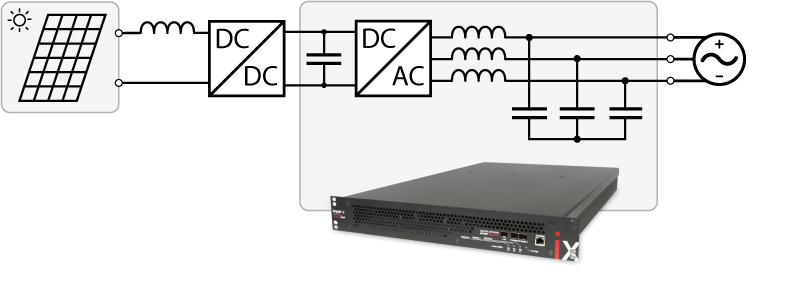
Grid Following Solar Inverter
A typical use-case scenario of the programmable inverter is to interface photovoltaic panels with the AC grid. In this application, the DC bus is precharged from the AC side, taking advantage of the automated precharge circuit.
Grid Forming Inverter with battery storage
Another use case is a grid-forming inverter based on a battery energy storage system. Voltage and current sensors are strategically placed to facilitate the implementation of a cascaded voltage control, typically used as the inner loop of a droop control algorithm.
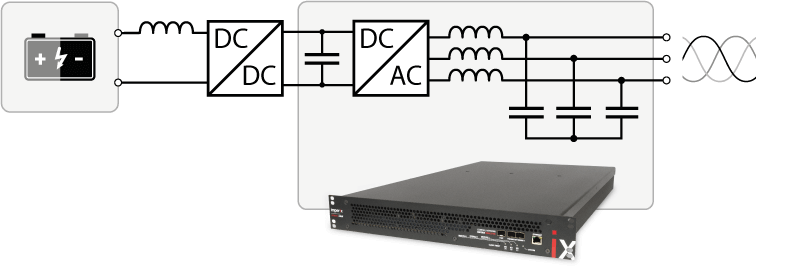
Intuitive programming with automated code generation
A fully programmable inverter

High-performance embedded controller
The embedded B-Board PRO controller uses a dual-core processor (Xilinx Zynq). One DSP core is dedicated to the real-time control tasks (bare metal, dedicated kernel), the other one to the system supervision and monitoring (Linux). Most low-level tasks are also shifted in FPGA.
This results in the full dedication of a fast floating-point processor (DSP) to power converter control purposes, with tremendous performance, ranging up to 400 kHz control frequencies in closed-loop operation.
Graphical programming with Simulink or PLECS
The programmable inverter can be programmed using simulation softwares such as Simulink or PLECS. Thanks to our fully-automated code generation toolchain, just one single click is needed to fully program the device!
The blocksets also embed simulation models so that the system can be accurately simulated and tuned before code is generated.
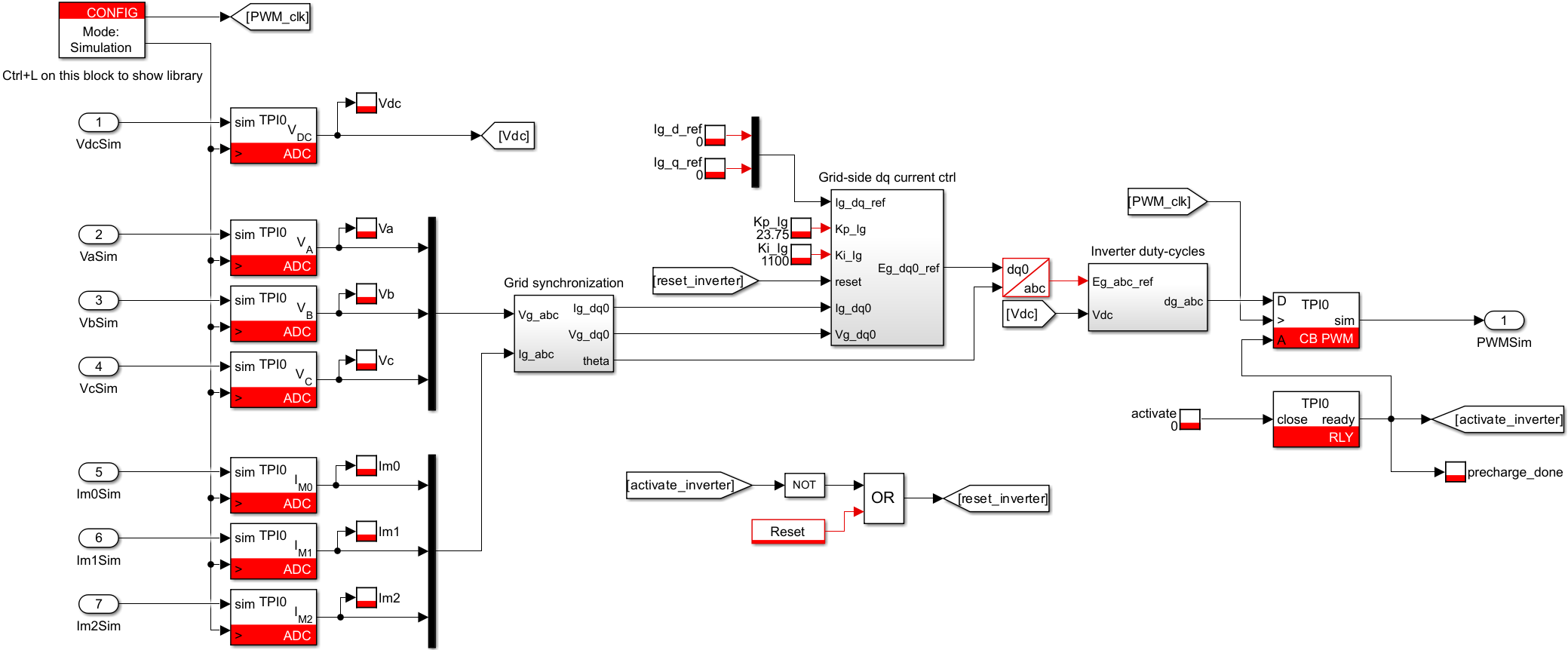

User-programmable FPGA
Absolutely no expertise in FPGA-based development is needed to work with the programmable inverter. It operates readily with a very flexible and entirely configurable FPGA firmware.
Nevertheless, for advanced users who require custom FPGA code, the embedded controller allows doing so. Dedicated FPGA areas are provided, with straightforward integration with DSP software.
Real-time monitoring software
During operation, Imperix Cockpit allows observing, editing, and logging any variable present in memory. This facilitates the rapid debugging and tuning of any converter control code.
- Real-time tuning of all variables
- 2 million points datalogging
- Free maintenance
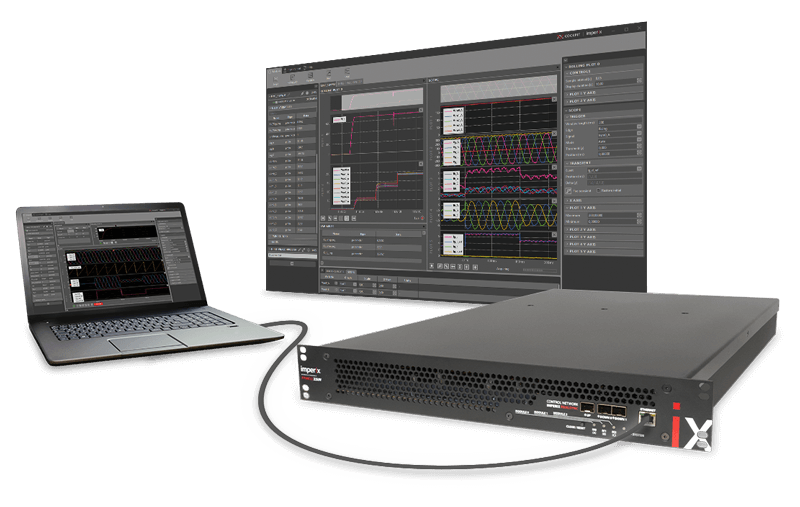
Connectivity and internal layout
The programmable inverter is designed to be integrated into a 19″ rack cabinet. With its slim and compact enclosure, the inverter optimizes the use of space by favoring depth rather than height. Furthermore, the analog and digital connectivity provided at the rear of the rack makes it simple to add external sensors, relays, etc. Finally, the programmable inverter can communicate with other devices over SFP, ethernet, or CAN.


Front view

Rear view

Internal layout
Integrating distributed energy resources into a smart grid
Research topic examples
- Droop control
- Virtual inertia
- Low voltage ride-through
- Anti-islanding
- Frequency-watt control
- Volt/VAR curves
- Synchrophasor estimation
- Virtual power plant
- Decentralized control
- Load shifting
- Model Predictive Control for battery storage
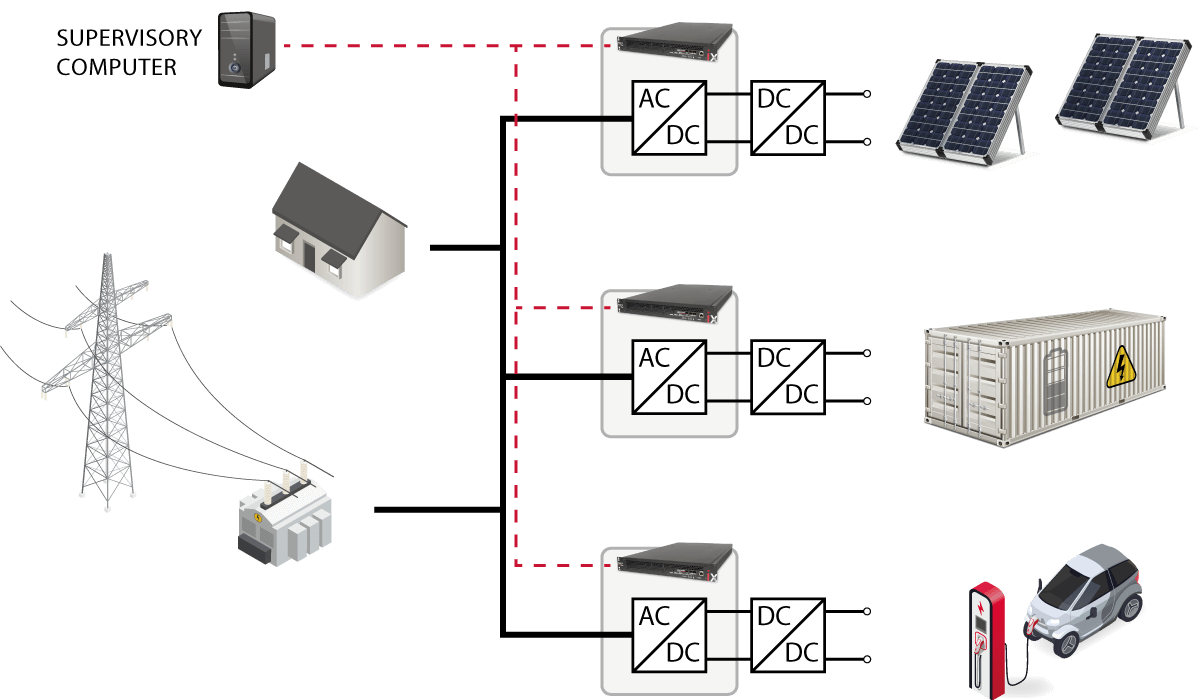
Grid support capabilities
State-of-the-art DERs are able to support the grid using various software-based techniques, which can be quickly implemented on the programmable inverter. It includes, for example, reactive power regulation using Volt/VAR curves or active ride-through strategies to withstand voltage and frequency disturbances.
Optimal energy management
The embedded B-Board controller offers plenty of processing power to tackle optimization problems. One such example is the energy management of a battery storage system based on Model Predictive Control (MPC). In fact low-level tasks (e.g. voltage/current control) can be implemented in FPGA to free up CPU time.
Distributed microgrid control
Multiple programmable inverters can operate as part of a control network using the imperix RealSync protocol for ultra-fast data exchanges. Alternatively, communication over ethernet is possible with third-party controllers, such as a Supervisory Control and Data Acquisition system (SCADA) master unit.
Modular alternatives to the programmable inverter
Kits and bundles
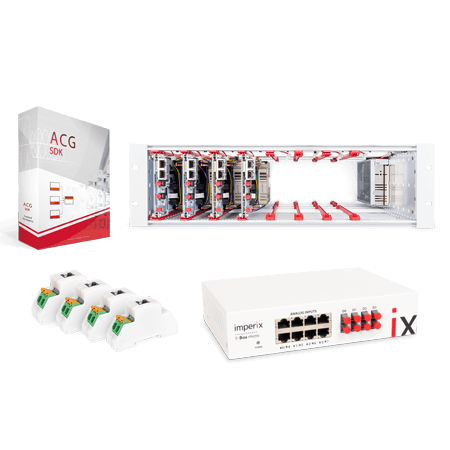

HARDWARE + SOFTWARE
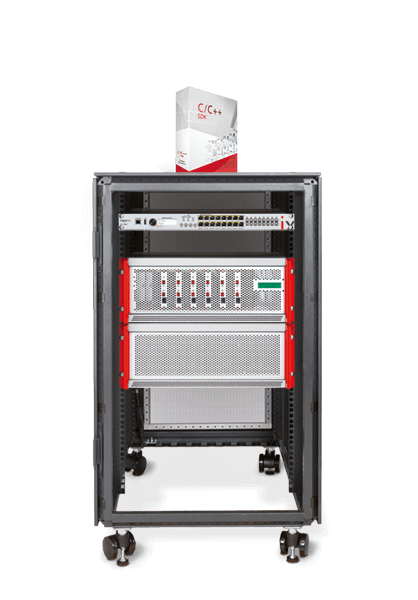

HARDWARE + SOFTWARE
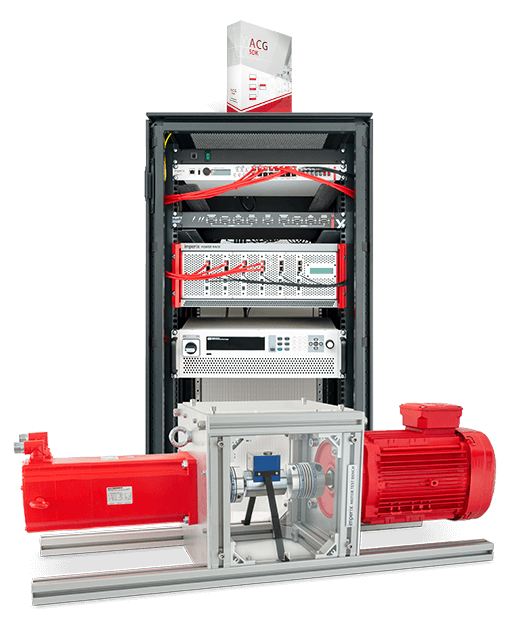

HARDWARE + SOFTWARE