
Inverter control board
B-Board PRO
Embedded converter controller
The B-Board PRO is an embeddable inverter control board that can be fully programmed using Simulink, PLECS, or C/C++. It operates identically to the B-Box RCP and B-Box Micro.
![]() | your price |
Fully-programmable inverter control board for product-embedded applications
Embedded control module
Our programmable converter control module, based on Xilinx Zynq, can have both its DSP and FPGA sections fully customized using our software development environment. It is ideally suited for demanding power electronic applications and advanced converter control techniques, which require powerful computational capabilities and complete software/firmware flexibility.
Typical applications include industrial inverters and rectifiers, motor drives, multilevel inverters, and all or distributed control systems. That said, our inverter control module can be involved in almost all applications where a fully programmable digital controller is needed.


Use B-Box RCP for your R&D activities
Our rapid prototyping controller offers the very same performance as the control module, but with some additional flexibility that is tailored for R&D purposes, contributing to accelerating product development.
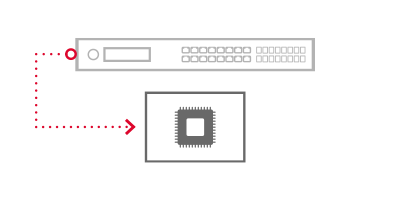

Migrate easily to B-Board PRO
Thanks to the exact equivalence between both programmable controllers, control software that was previously developed on B-Box RCP can be instantly ported on B-Board. In fact, the very same bitfile can be used!


Use B-Board PRO for your products
The B-Board PRO possesses just what is needed for embedded control applications. It is small enough to be integrated directly within power converters, yet powerful enough to support advanced applications.
Development phase
- Flexible hardware
- Rapid control validation
Production phase
- Cost-optimized hardware
- Product integration


B-Board PRO
Inverter control board

B-Box RCP
Prototyping controller
The exact compatibility between B-Box RCP and B-Board PRO allows benefitting from the increased flexibility of the prototyping controller during developments, while using a product-embeddable variant during series production.


Development phase
Rapid prototyping controller
- Flexible hardware
- Rapid control validation

Production phase
Inverter control module
- Cost-optimized hardware
- Product integration

B-Box RCP Prototyping controller
The exact compatibility between B-Box RCP and B-Board PRO allows benefiting from the increased flexibility of the prototyping controller during developments while using a lower-cost product-embeddable inverter control board during series production.

Full bitfile compatibility!

B-Board PRO Inverter control board


A power converter controller, equivalent to B-Box RCP!
The embeddable inverter controller module possesses most features of its laboratory counterpart, except the configurable analog front-end and the software-independent protections.
It is meant to be a cost-optimized equivalent system for embedded control applications, fully cross-compatible with its larger sister.
B-Box RCP | B-Board PRO | |
---|---|---|
Processor (Xilinx Zync) | 2x ARM 1GHz | 2x ARM 1GHz |
FPGA (Xilinx Zynq) | Kintex 7 125K | Kintex 7 125K |
Analog to digital converters | 16x | 8x |
C++ programming | ||
Simulink programming | ||
Programmable front-end | ||
Hardware protections |
Key hardware specifications
System on chip | Xilinx Zynq XC7Z030-3FBG676E | Digital outputs | 16x Electrical (3.3V) |
Processor | 2x ARM Cortex A9 1GHz | Digital inputs | 16x Electrical (3.3V) |
FPGAs | Xilinx Kintex 7 125K (user programmable) | Fault inputs | 16x Electrical (1.8V) 1x Electrical interlock |
Analog inputs | 8x 16bits @2Msps | Incremental decoder inputs | 4x 3-pins (A,B,Z) (shared with GPI inputs) |
PWM outputs | 16x Electrical (1.8V) 16x Electrical (3.3V) | Communication | 1x USB 2.0 (computer) 1x Ethernet 1Gbps (RJ45) 3x SFP+ 5Gbps 1x CAN + user high-speed I/Os |
User High-speed I/Os | 36x Electrical (3.3V) |
System on chip | Zynq XC7Z030-3FBG676E |
Processor | 2x ARM Cortex A9 1GHz 1GB DDR3 |
FPGAs | Kintex 7 125K (user programmable) |
Analog inputs | 8x 16bits @2Msps |
PWM outputs | 16x Electrical (1.8V) 16x Electrical (3.3V) |
User High-speed I/Os | 36x Electrical (3.3V) |
Digital outputs | 16x Electrical (3.3V) |
Digital inputs | 16x Electrical (3.3V) |
Fault inputs | 16x Electrical (1.8V) 1x Electrical interlock |
Encoder inputs | 4x 3-pins (A,B,Z) (shared with GPI inputs) |
Communication | 1x USB 2.0 (computer) 1x Ethernet 1Gbps (RJ45) 3x SFP+ 5Gbps |
An embeddable inverter control board
The B-Board PRO is a small piggy-back control module meant to be assembled within a larger converter control system. It embeds the essential and application-independent part of a power converter controller and can be easily mounted on top of a system-specific carrier board.
Bitfile compatibility
The inverter control module is guaranteed to work exactly the same way as the B-Box RCP, with the exact same performance. In fact, the very same bitfile can be used on both devices.
Small form factor
Despite its numerous I/Os, the control module measures only 86×124 mm. This is small enough to be assembled in most industrial systems. It also fits within a headroom of 22mm only!
Processing power
The embeddable control module is exactly as powerful as the B-Box RCP. Indeed, with its dual-core 1GHz processor, it features outstanding performance, especially for an embedded controller.
Extensive I/O connectivity
Everything needed to control advanced power inverters!
Over 120 user I/Os
The inverter control module is ready for the most demanding needs and has been specially designed with low- to mid-volume, complex applications.
With its high number of digital I/Os, there’s plenty of extension margin. The application scope is thus mostly defined by the available analog inputs.
Ideal for distributed control applications!
When needed, hierarchized or distributed control systems can also be implemented. This allows either building larger control systems or interconnecting several programmable controllers together.
Communication can be implemented easily over Ethernet, CAN, or our proprietary low-latency protocol running over optical fiber links (SFP).
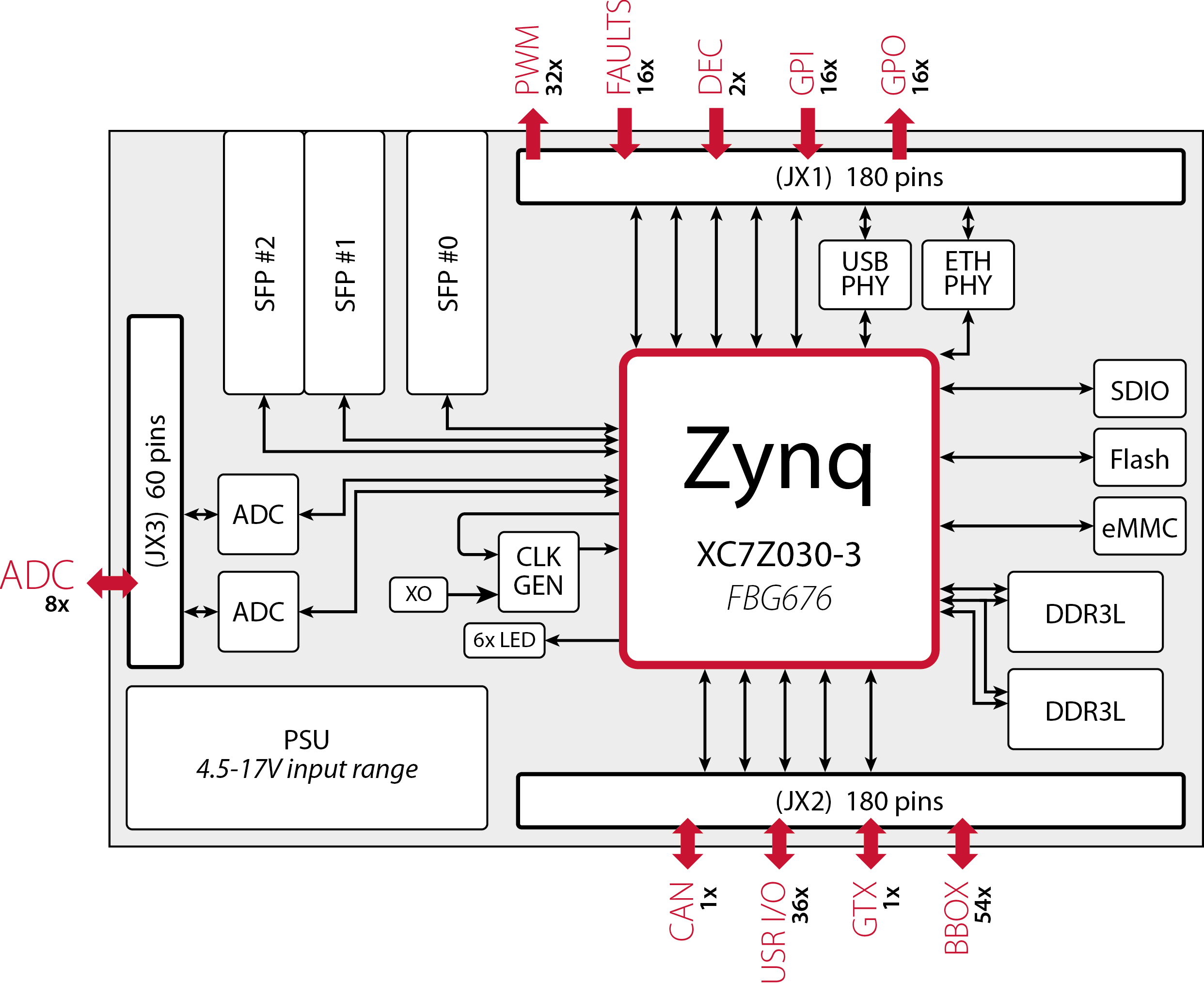
The inverter control module offers plenty of I/O connectivity with other industrial control equipment.
Benefits for industrial applications
A powerful converter control board
The B-Board PRO inverter control board brings most of the benefits of a rapid prototyping system directly into industrial applications. When compared to the B-Box RCP or B-Box Micro, it offers the same development environments, exact same performance, and same remote access capabilities.
Integrated with Simulink and PLECS

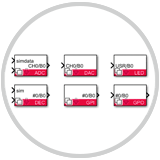
The converter controller can be programmed using C/C++ code, or directly from simulation software, such as Simulink and PLECS. Thanks to a fully automated code generation toolchain, just one single click is all it needs to fully program the device!
The provided blocksets also embed simulation models so that the system can be accurately simulated and tuned before run-time is generated.
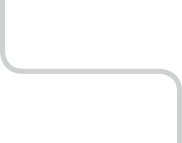
Absolutely no expertise in FPGA-based development is needed to work with this industrial control module. It operates readily with a highly flexible and highly configurable FPGA firmware.
Nevertheless, for the advanced users who require to alter the FPGA code, the B-Board PRO allows doing so. In this case, dedicated areas are provided, with straightforward integration within the existing DSP software kernel.
User-programmable FPGA


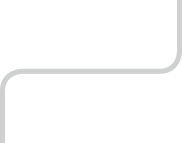
Up to 400kHz closed-loop rate

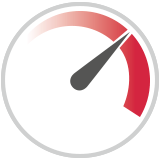
The converter control module uses a dual-core processor. One core is dedicated to the execution of the closed-loop control tasks (bare metal, dedicated kernel), the other one to the system supervision and monitoring (linux). Most low-level tasks are also shifted in FPGA.
This results in the full dedication of a fast floating-point processor core to real-time control tasks, with best-in-class performance, ranging up to 250kHz control frequencies in closed-loop operation.

In addition to being 100% compatible with the prototyping controller, the inverter control board benefits from the same software environment and tools. It, therefore, facilitates debugging and testing activities in the same way!
Overall, integration efforts are often limited to mechanical aspects, which are specific to the application anyway. All the rest is in direct continuity with previous work done with the B-Box RCP.
Quick product integration
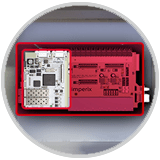

Benefits for industrial applications
A powerful inverter controller
The inverter control board brings most of the benefits of a rapid prototyping system directly into industrial applications. When compared to the B-Box RCP or B-Box Micro, it offers the same development environments, exact same performance, and same remote access capabilities.
Inverter control development from Simulink and PLECS
![]() | ![]() |
The power electronic inverter controller board can be programmed using C/C++ code, or directly from simulation software, such as Simulink and PLECS. Thanks to a fully automated code generation toolchain, just one single click is all it needs to fully program the device!
The provided blocksets also embed simulation models so that the system behavior can be accurately simulated and tuned before run-time is generated.
Inverter control module with user-programmable FPGA
![]() | ![]() |
Power electronic engineers need absolutely no expertise in FPGA-based development to work with the B-Board inverter control module. It operates readily with a highly flexible and highly configurable FPGA firmware.
Nevertheless, for the most advanced users who require to alter the FPGA code, the B-Board control module allows doing so. In this case, dedicated areas are provided, with straightforward integration within the existing DSP software kernel.
Digital control board with fast processors
![]() | ![]() |
The B-Board PRO inverter control board uses a dual-core processor; one core being dedicated to the execution of the closed-loop control tasks (bare metal, dedicated kernel), the other to the system supervision and monitoring (linux). Besides, most low-level tasks are shifted in FPGA.
This results in the full dedication of a fast floating-point processor core to real time control tasks, with best-in-class performance, ranging up to 250kHz control frequencies.
Quick integration into power inverters
![]() | ![]() |
In addition to being 100% compatible with B-Box RCP, the B-Board PRO inverter controller board benefits from the same software environment and tools. It can be programmed from Simulink (or PLECS) and controlled from Imperix Cockpit too!
Overall, most of the specific integration efforts are only those related to the mechanical aspects as well as the signal conditioning and protection, which are often tailored to the application anyway.
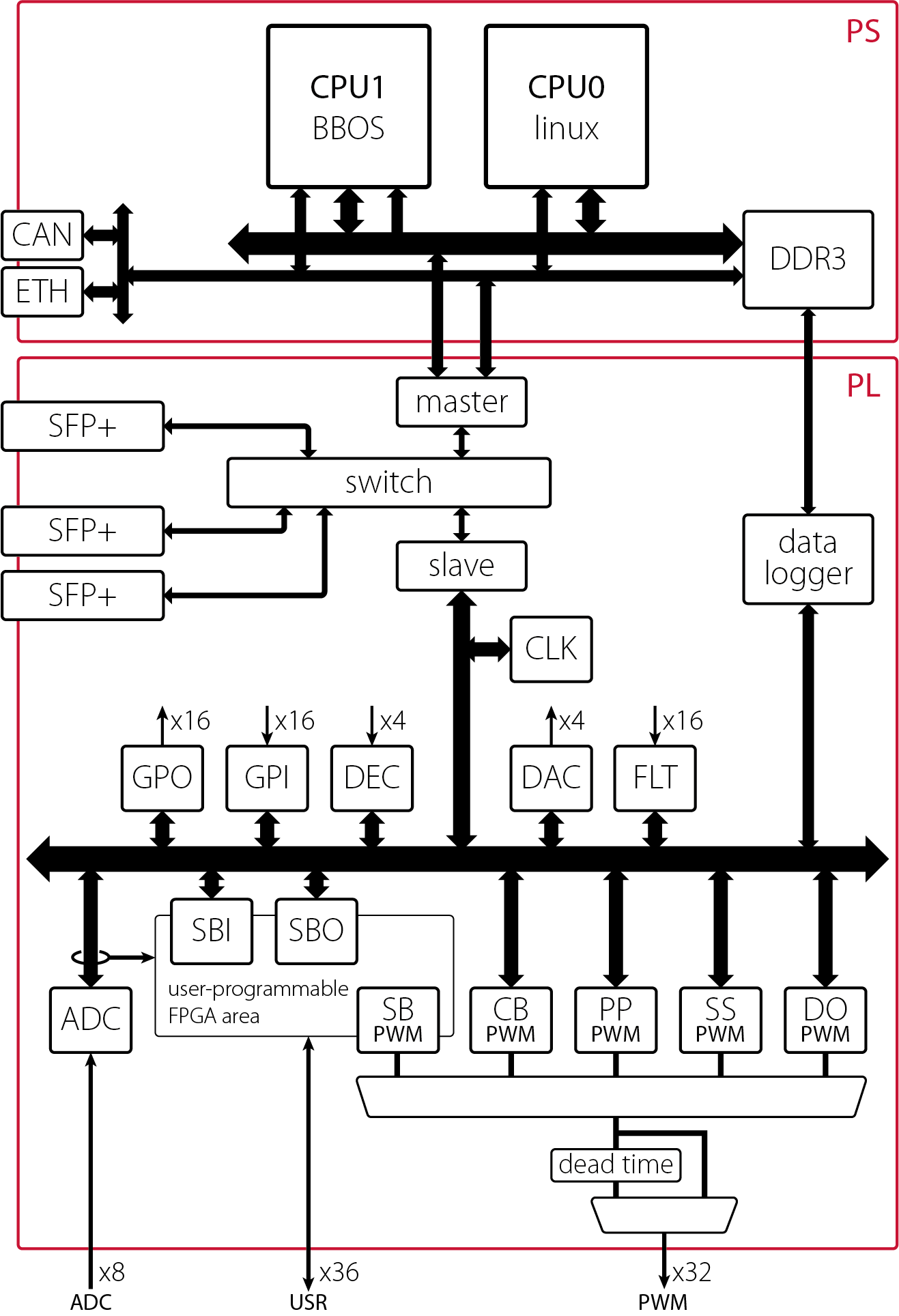
The inverter control board embeds a specialized operating system and firmware for power inverters.
A specialized operating system for power electronics
High performance and safety
The inverter controller board embeds an ultra-light operating system (BBOS), specially tailored for hard real-time applications. This kernel simultaneously combines a high level of safety, very low overhead, and very rigorous management of priorities.
Integrated monitoring capabilities
The B-Board PRO control module also benefits from the close interaction of BBOS and the second CPU core (Linux) for debugging, monitoring, and the related interaction with the remote computer. This non-invasive supervision can also be used for long-term remote surveillance.
Hardware independence
Thanks to its fully FPGA-based peripherals, the B-Board is built on a strong hardware abstraction layer. As such, any control code is guaranteed to keep working across future generations of hardware, facilitating system maintenance and upgrade.
Comprehensive computer software
Tools dedicated to the control of power converters
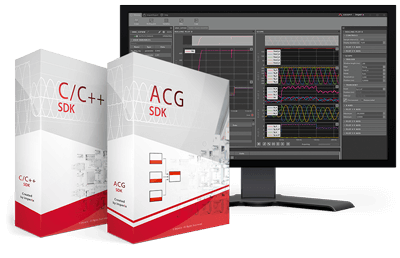
Comprehensive design suites
Rapid control prototyping with our programmable controllers is supported by our software development kits (SDK), for either C++, Simulink or PLECS.
- Support for C++, Simulink, or PLECS
- Code libraries/examples
- Free maintenance
Monitoring & control software
During operation, Imperix Cockpit allows observing, editing and logging any variable. This facilitates the rapid debugging and tuning of any converter control code.
- Real-time tuning of all variables
- 2 million points datalogging
- Free maintenance
The Evaluation kit allows quickly evaluating
the tremendous capabilities of the B-Board PRO.
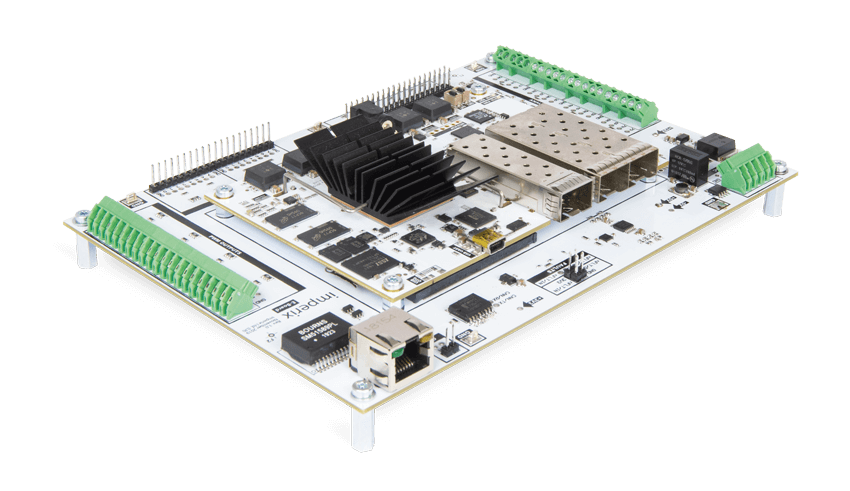
Evaluation kit
Discovery and development kit for B-Board PRO
The Evaluation kit enables development engineers to power up the B-Board PRO and get the first signals out of it within few minutes. It notably contains an easy-to-use carrier board that gives instant access to most analog and digital signals, normally located on the bottom of the embedded control module.
The kit also contains suitable documentation and getting-started examples as to best support a rapid evaluation of the hardware and software capabilities, featuring the very same performance as B-Box RCP system.
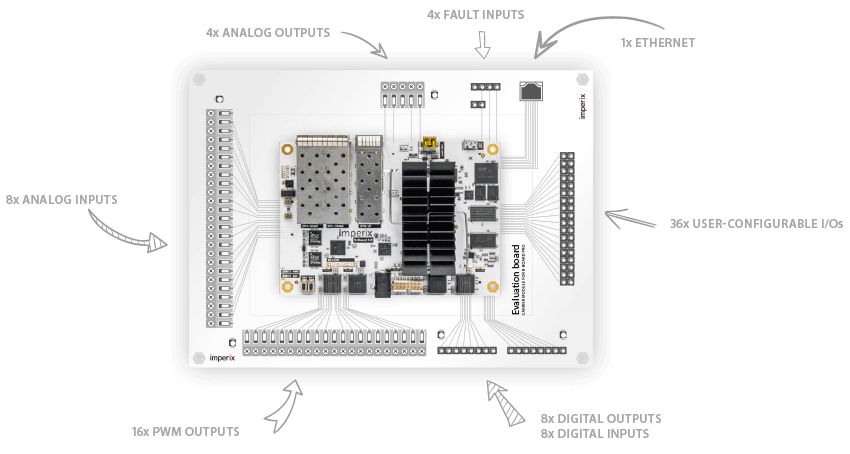
carrier board signals
x8 | Analog inputs | Full-differential inputs,16bits | Phoenix 3.5mm (1989023) | ± 5V |
x4 | Analog outputs | 16bits, single-ended | Phoenix 3.5mm (1989023) | ± 5V |
x1 | Fault input | Electrical | 2.54 mm header | 3.3V |
x1 | Communication | Ethernet, device programming and monitoring | RJ45 socket | |
x16 | PWM outputs | Dedicated modulators, 4 differents time bases | Phoenix 3.5mm (1989023) | 3.3V |
x8 | Digital outputs | 2.54 mm header | 3.3V | |
x8 | Digital inputs | 2.54 mm header | 3.3V | |
x36 | User configurable I/Os | Direct to FPGA, bidirectional | 2.54 mm header | 3.3V |
x8 | Analog inputs | Full-differential inputs,16bits Phoenix 3.5mm (1989023) | ± 5V |
x4 | Analog outputs | 16bits, single-ended Phoenix 3.5mm (1989023) | ± 5V |
x1 | Fault input | Electrical 2.54 mm header | 3.3V |
x1 | Communication | Ethernet, device programming and monitoring RJ45 socket | |
x16 | PWM outputs | Dedicated modulators, 4 differents time bases Phoenix 3.5mm (1989023) | 3.3V |
x8 | Digital outputs | 2.54 mm header | 3.3V |
x8 | Digital inputs | 2.54 mm header | 3.3V |
x36 | User configurable I/Os | Direct to FPGA, bidirectional 2.54 mm header | 3.3V |
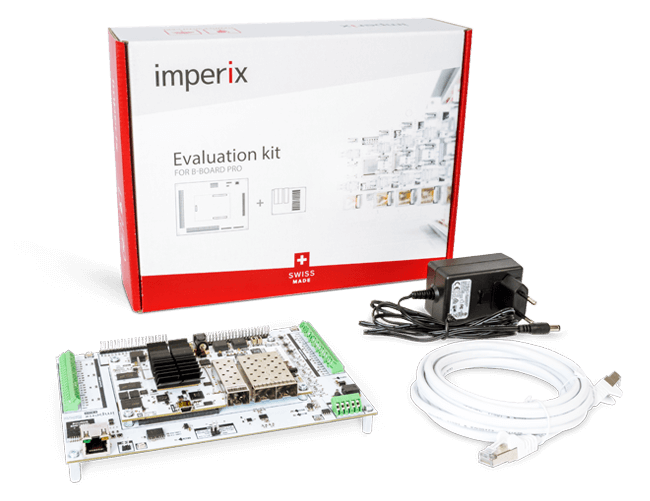
CONTENT OF THE KIT | |
---|---|
Carrier board (motherboard) | x1 |
B-Board PRO | x1 |
Power supply (20W / 12V) | x1 |
Ethernet cable | x1 |
Quick start guide (user manual) | x1 |
![]() | your price |

![]() | ACG SDK your price |
![]() | C/C++ SDK your price |