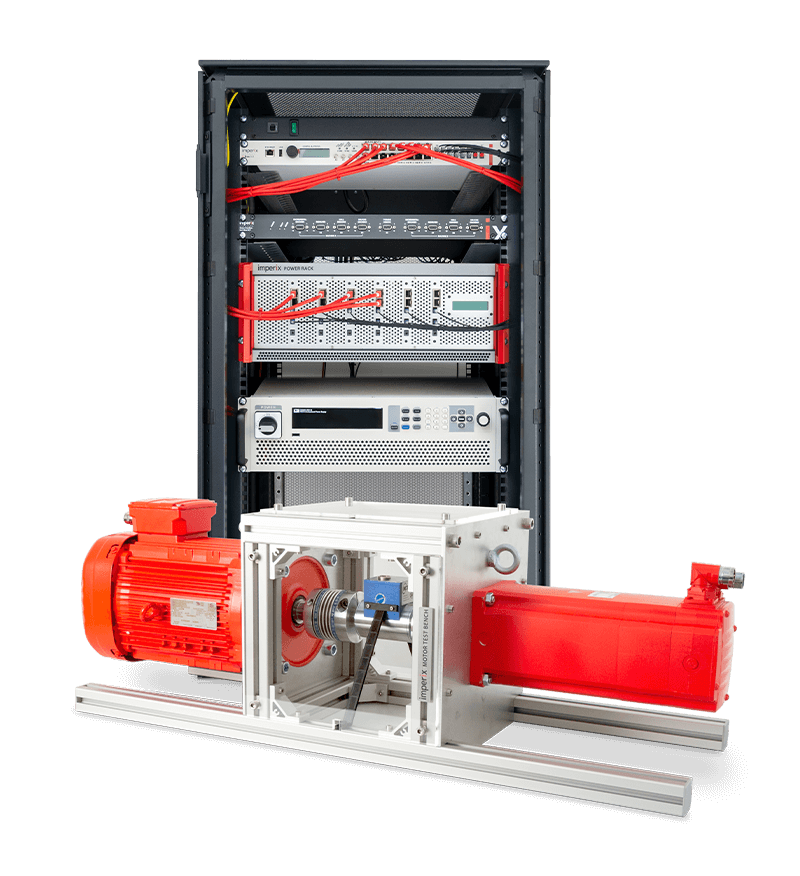
Bundle content
- 1x B-Box RCP
- 1x Motor Interface
- 6x SiC power modules
- 1x DC source
- 1x Induction machine
- 1x Synchronous machine
- Blockset for Simulink
Electric motor drive bundle
Ready-to-use test bench for motor drive applications
The Electric Motor Drive Bundle is a complete solution for electric motor control prototyping. It includes a fully programmable motor drive combined with a pair of 4kW motors.
The system is a ready-to-use platform to validate control techniques for high-performance variable speed drives. It comes with turnkey code examples to get started with the provided motors in no time.
The flexibility of imperix solutions allows modifying the code examples and even reprogramming the entire control algorithm from scratch if needed. Similarly, the modular hardware is reconfigurable afterward to create new electric motor drive topologies.
![]() | your price |
From an idea to a fully functional prototype
What is the electric motor drive bundle?
The Electric Motor Drive Bundle is a ready-to-use reduced-scale prototype for control engineers. It features a fully programmable drive combined with a dual-motor test bench. The complete system easily fits in a laboratory and does not require any cumbersome infrastructure to operate. Plug the motor drive into a three-phase power outlet and start experimenting!
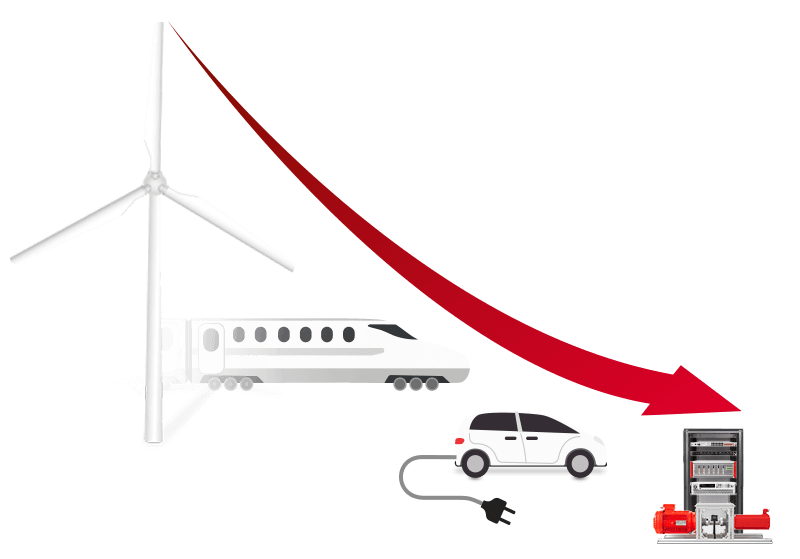
A motor drive system at the scale of your laboratory
Building a real-scale prototype of an electric motor drive system is time-consuming and expensive. It is especially true for large systems such as the electric propulsion of a car or a wind turbine generator.
A common trick to accelerate the development process is to validate the design on a functional prototype first.
Key technical specifications
- 4 kW electric machines
- 1800 rpm nominal speed
- Up to 800VDC operation
- 23.8 Nm maximum torque
PLUG-&-PLAY
The Electric Motor Drive Bundle is a ready-to-use solution for motor control prototyping. It includes an electric motor drive, a pre-built motor test bench, and turnkey code examples.
FULLY PROGRAMMABLE
The digital controller allows the implementation of the most advanced control techniques on both the DSP and FPGA. Programming is possible using Simulink, PLECS, or C/C++ code.
SELF-PROTECTED
The built-in hardware protections are user-programmable and instantaneously switch off the power stage to prevent inappropriate operation. A brake is also available for emergency braking.
Default hardware configuration
Back-to-back machines arrangement
First electric machine
Device Under Test (DUT)
The first machine plays the role of the device under test (DUT). Take advantage of the fully reprogrammable B-Box RCP controller and replicate the functionalities of the real-scale system.
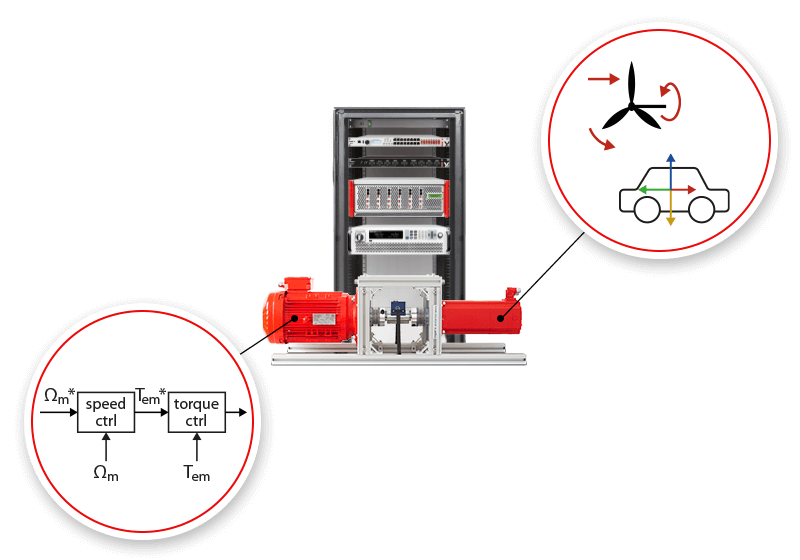
Second electric machine
Environment modeling
The second machine of the test bench acts as a programmable load. Its purpose is to produce realistic load conditions for the DUT. Create a physical model of your system in the digital controller and scale it down to the ratings of the test bench.
Everything you need for experimental validation
What is included in the electric motor drive bundle?
DEFAULT EQUIPEMENT SET
Essential elements of the motor drive bundle
The bundle includes all necessary equipment to operate two machines in a back-to-back configuration. It covers the entire motor-drive system from the digital controller to the power stage and the motors.

POWER INVERTERS
DIGITAL CONTROLLER
The digital controller is fully programmable, and the Motor Interface extension provides additional functionalities for electric motor drive applications.
MOTOR TEST BENCH
Both machines can either play the role of the DUT or load. It also embeds position, torque, and temperature sensors, as well as an emergency brake.
POWER SUPPLY
The reversible power supply sources or sinks power to/from the electric motors. Thus, regenerative operation of the machines is possible.
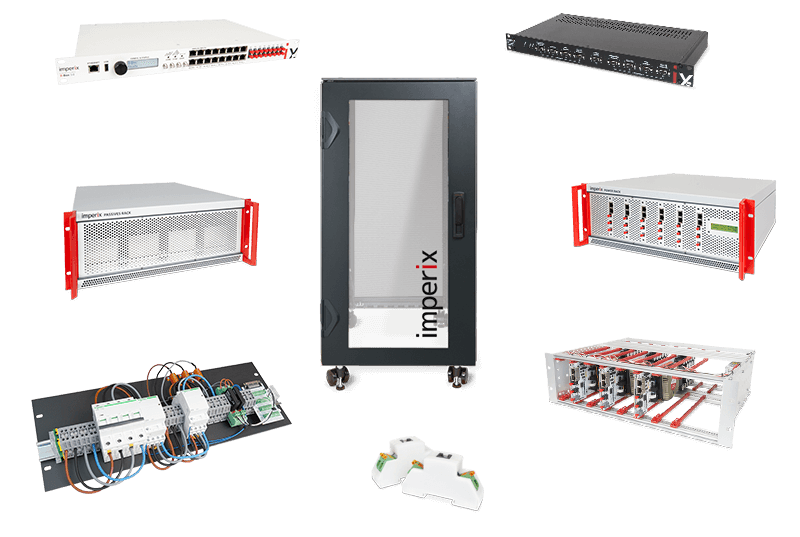
OPTIONAL ELEMENTS
Tailored solutions from imperix standard products
Imperix standard products offer a high degree of modularity, allowing rearranging the hardware configuration of the electric motor drive to your needs. This approach dramatically reduces costs since it does not require custom hardware development. Additionally, research engineers can modify the motor drive topology on their own with our user-friendly hardware.
Upon request, our technical staff can prepare the hardware configuration of your choice. Contact us for more information and receive your tailored solution pre-assembled.
Test your electric motor drive on actual machines
Motor Testbench
Spin real motors in your lab
While simulation provides meaningful insights into the operation of a system, experimental results are still the only way to validate a control algorithm. Unfortunately, building a motor prototyping setup requires significant work for the mechanical design.
Imperix offers a turnkey solution to bypass this inconvenience and start spinning real motors in no time. The Motor Testbench is a pre-built system featuring two industrial-grade machines. Forget about mechanics and jump straight into control algorithm design.
- 4 kW squirrel cage induction machine
- 4 kW permanent magnet synchronous machine
- Bidirectional torque sensor
- 2x PT1000 temperature sensors
- Resolver (position sensor)
- Built-in brake
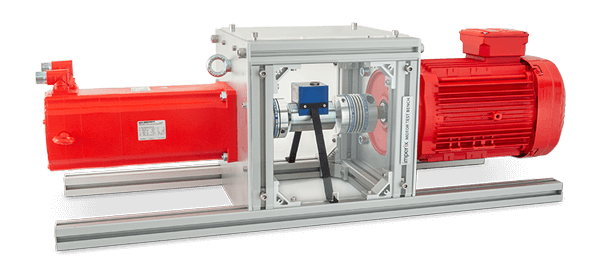
Safety features
Some motor drive systems make use of a mechanical brake for safety purposes. Typical use cases include locking an elevator in place in case of a power failure or performing an emergency braking with an electric vehicle. Thus, the Motor Testbench features a built-in brake to perform these functions if needed.
The machines are mounted on a robust aluminum frame to absorb vibrations and abrupt torque variations. Additionally, transparent protective plates enclose the shaft to prevent accidental access to spinning parts during operation. Finally, each motor has a built-in temperature sensor to monitor the temperature of the windings.
I/O connectivity for your electric motor drive
Motor Interface for B-Box RCP
One interface to connect them all
Motor drive applications often require measuring mechanical quantities such as position and torque. The temperature of the windings is also a variable of interest since the machine parameters depend on it.
For these applications, the Motor Interface for B-Box RCP extends the I/O of the controller and supports a wide variety of motor sensors (from the Motor Testbench or other machines). This interface provides all the necessary signal conditioning and power supplies required by these external sensors.
- 2x Incremental encoder interfaces
- 2x Resolver interfaces
- 2x Hall sensors interfaces
- 2x Sin / cos interfaces
- 2x Temperature sensor interfaces
- 1x Torque sensor interface
- 1x 24 Vdc brake command
- 1x Electrical interlock
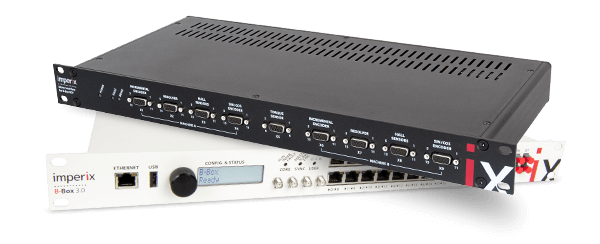
An extension of the B-Box RCP
The B-Box RCP communicates with the Motor Interface through a single VHDCI cable. From a user perspective, the functionalities provided by the interface are available through the imperix standard library like any other resources built into the B-Box RCP.
The Motor Interface improves the safety features of the B-Box RCP in the context of electric motor drive applications. It includes a brake control unit, which can be linked to an emergency stop button.
Explore our knowledge base
Electric motor drive applications
The knowledge base offers numerous references, including application examples, turnkey control files, technical notes, and general product guidance. By browsing the knowledge base, research engineers are never short of help when working with the Electric Motor Drive Bundle.
- Sensorless speed estimation
- Scalar control (V/f)
- Field oriented control (FOC)
- Direct torque control (DTC)
- Vector current control
- Field weakening strategy
- Highspeed operation
- Inertia emulation
- Different machines (PMSM, BLDC, IM, SRM, …)
- Multi-drive coordination
- etc.
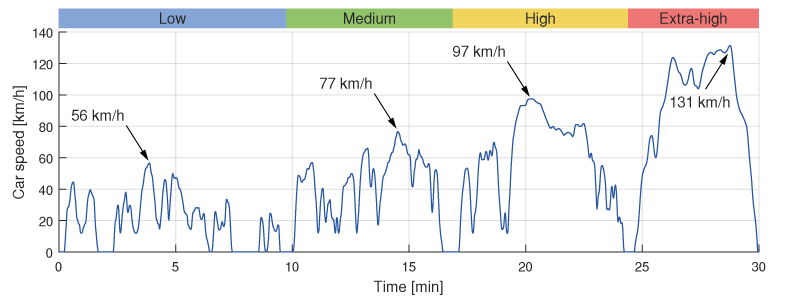
TYPICAL USE CASE SCENARIO – WLTP STANDARD TEST CYCLE
The Worldwide harmonized Light vehicle Test Procedure (WLTP) is a standard driving test cycle used to compare passenger car performances across the globe. When using the Electric Motor Drive Bundle to perform a WLTP test, one machine plays the role of the electric car motor, while the other one emulates realistic load conditions (effect of the air drag, inertia of the car, …).
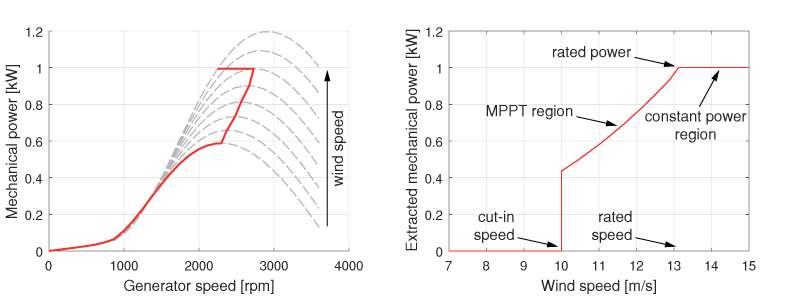
ADDITIONAL USE CASE SCENARIO – WIND TURBINE EMULATION
The mechanical power of a wind turbine depends on several factors, such as the wind speed, the pitch of the blades, and the generator speed. Emulate the physics of the wind turbine and evaluate the impact of environmental conditions on your control strategy. Safely test challenging wind conditions thanks to the down-scaled ratings and built-in protections of the Electric Motor Drive Bundle.