
PLECS BLOCKSET
Part of the ACG SDK
The PLECS blockset contained within ACG SDK enables graphical converter control software design and implementation. It transforms imperix controllers into fully-compatible PLECS Coder targets.
The blockset takes advantage of both the simulation and code generation engines of PLECS to support easy converter control development and maintenance.
MAIN BENEFITS
- Ease of use: Accessible and fast graphical programming thanks to automated code generation.
- Accurate modeling: Advanced simulation models for faithful offline simulation results.
- Extensive capabilities: Broad range of specialized functions such as ADC, PWM modulators, etc…
- High performance: Transparent use of optimized driver methods for uncompromised performance.
- High flexibility: Easy integration with custom FPGA-based developments, offering boundless possibilities.
![]() Create PLECS model Start from scratch, adapt an existing control model, or use one of the code examples available on the imperix knowledge base. |
![]() Run offline simulation You can test your control on a simulated converter model first. Then, you can rely on the obtained results to switch to real power. |
![]() Auto-generate code In just one click, your model is automatically converted into code and executed on your imperix target, thanks to a fully integrated toolchain. |
![]() Capture results The transient generator and datalogging features of Cockpit will challenge your control and export the results for your next publication. |
Integrated control software development
The ACG SDK can integrate directly inside the PLECS environment, making rapid prototyping directly available from PLECS – standalone or blockset – which offers:
- A vast collection of PLECS native blocks
- Native libraries. Including electrical, thermal and magnetic libraries
- A powerful simulation and code generation engines
On the control side, the ADG SDK makes imperix controllers directly programmable from PLECS. Each block contains both a simulation model and its code counterpart for the real-time execution.
On the plant side, PLECS can be fully leveraged for running offline simulations and pre-tuning control parameters, making the transition from the computer to the lab quick and easy.

EMBEDDED OPERATING SYSTEM
Thanks to the layered structure of the embedded operating system, PLECS has access to the exact same drivers as the C++ routines. This guarantees the best possible performance as well as a rigorous supervision of possible hardware misconfigurations.
FPGA CUSTOMIZATION
For demanding applications, parts of the runtime control can be offloaded inside the user-programmable portion of the FPGA. For this, PLECS has interface blocks readily available, exchanging data with the FPGA sandbox (SBI and SBO peripherals).
SOFTWARE LICENSING
The licensing policy of ACG SDK authorizes downloading and installing the software on an unlimited number of computers. As such, offline simulation is always possible. A license is only required to load and execute the control code onto a real-time control target (e.g. B-Box).
Interface blocks to dedicated hardware peripherals
The PLECS blockset included in ACG SDK contains numerous blocks to interface your PLECS model with any kind of I/O on imperix controllers. In particular, several PWM modulators are provided to fulfill the needs of the most demanding applications, whether it is for a traditional carrier-based or a more advanced multi-level modulator.

CB-PWM Conventional pulse-width modulators with fixed or variable phase-shift. |
Direct update of switching state output. |
SV-PWM Two- and three-level Space Vector modulator. |
SB-PWM Configurator for custom modulators designed in the FPGA Sandbox. |
SS-PWM Multilevel modulator and balancer for modular converter topologies (MMC and similar). |
PP-PWM LUT- based modulators for pre-optimized patterns such as selective harmonic elimination (SHE). |
ACCURATE Controller MODELING
Thanks to precise simulation models in every peripheral block, the behaviour of imperix controllers can be accurately anticipated, allowing you to test and tune control strategies offline. Ultimately, this means that the transition from simulation to real power is made as smoothly as possible.
To this end, we carefully modelled every aspect of the control loop, especially regarding its dynamic behaviour. This involves parameters such as the sampling instant or PWM phase-shift, but also the computation time of the algorithm or the conversion delay of the ADCs.

BOTH CONTROLLER AND PLANT IN THE SAME MODEL
Imperix examples are systematically constructed with two parts:
The control subsystem is meant to be executed in real-time on the controller. As such, it contains the peripheral blocks and the control algorithms, which can be automatically translated into executable code.
The plant subsystem contains a simulation model of the controlled equipment. This enables the accurate closed-loop simulation of the complete setup. However, no code is generated for that part.
SAMPLING INSTANT
The ADC block combined with the sampling clock signal ensure that the measurements provided by the plant model are sampled at the correct frequency and with the right phase. This way, the simulated controller can work with the exact same discrete samples as a real controller.
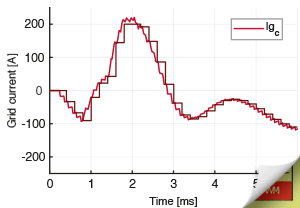
PWM PHASE-SHIFTS
The CB-PWM block lets you freely configure the phase-shift, even at run time. In addition, the corresponding simulation model uses a clock signal to guarantee a precise timing of the generated switching edges using the exact same logic as the real controllers.
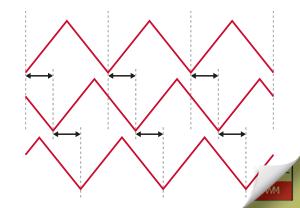
ACCURATE PLANT MODELING
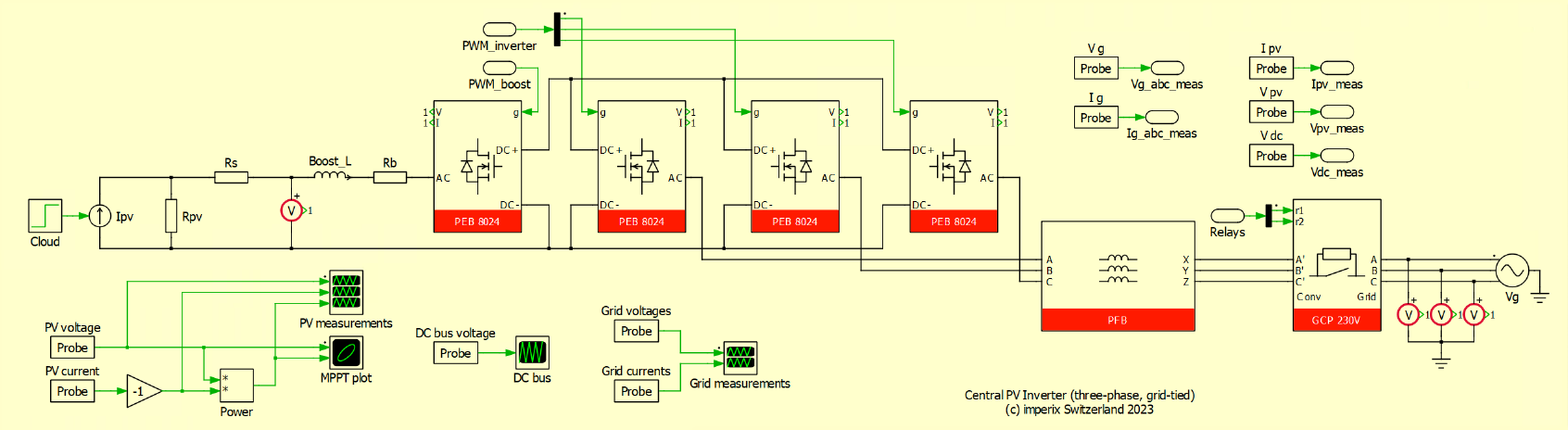
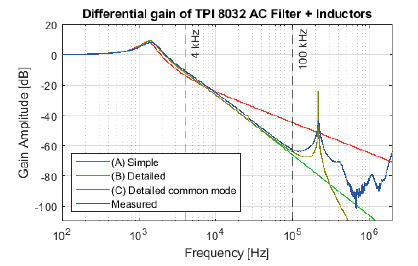
FREQUENCY MODELING
In order to faciliate the tuning of your control algorithms, the frequency-dependent behaviour of imperix products is accurately modeled.
Several levels of details are offered, corresponding to different trade-offs between accuracy and simulation complexity.
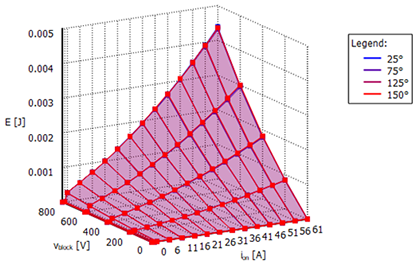
LOSSES MODELING
Both switching and conduction losses are accurately quantified, under various conditions, for most power products.
This enables the accurate anticipation of system-level efficiency, and is also ncessary for the proper evaluation of the safe operating area of our power modules.
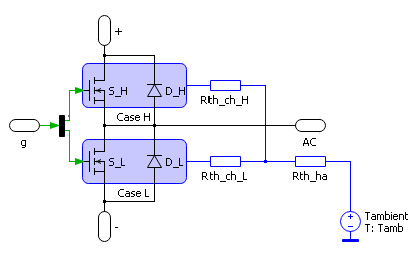
THERMAL MODELING
In order to precisely evaluate how much current can be carried under various operating conditions (e.g. as a function of the switching frequency, or under soft-switching conditions), the operating temperature must be evaluated.
Thermal simulation models of most power products is also included in the Power Library.