Table of Contents
What is an onboard battery charger?
An onboard battery charger (OBC) is an automotive power electronic converter tailored to charge an EV directly from the grid. As the name suggests, the onboard battery charger is integrated into the vehicle and is carried by the vehicle at all times. Because of this, researchers and Original Equipment Manufacturers (OEMs) are constantly innovating to ensure that OBCs become lighter and more efficient. A lighter onboard battery charger increases the range of the electric vehicle and a more efficient charger decreases the amount of energy wasted from the grid. This reduces the overall cost per mile for an EV driver.
While DC fast charging is an alternative to charging an EV using an OBC (see AN007 – Fast electric vehicle charger with intermediate energy storage for an example), the convenience of charging the vehicle from the much more accessible (including at home) AC grid is not to be underestimated.
Onboard battery charger design example
Design and control objectives
- An OBC must be able to control the battery charging current/voltage
- An OBC must be able to maintain unity power factor when charging the battery
- For safety, an OBC should be isolated from the grid
- As mentioned in the introduction, it should be small and light
In addition to the 4 core objectives, if the onboard battery charger is able to operate bidirectionally, it opens the door for vehicle-to-grid (V2G) applications as well.
When considering objectives 1 and 2 from the list above, a common solution is to consider two-stage converters, which simplify the decoupling of the two distinct controlled variables, namely the battery charge current, and the power factor from the grid [1].
Similarly, when considering objectives 3 and 4 from the list above, the design of the onboard battery charger is constrained to high-frequency isolation transformers because the weight and volume of a transformer are inversely proportional to its operating frequency. High-frequency transformers are common in isolated DC/DC converters, resulting in most onboard battery chargers having a non-isolated active rectification stage and an isolated DC/DC battery charging stage [1].
Typical topology
The two-stage approach shown in Figure 1 is a common configuration for onboard battery chargers. Multiple converter topologies can be implemented to achieve the control objectives of each stage, and the choice made depends on multiple factors such as controllability, cost to manufacture, targeted efficiency, etc.
Some examples are listed below:
PFC stage
- Boost PFC converter
- Bridgeless dual-boost PFC converter
- totem-pole PFC converter
Battery charger stage
- LLC converter
- DAB converter
- Full bridge converter
In addition, the choice between implementing a three-phase onboard battery charger (max 22 kW charging) and a single-phase version (max 7.4 kW charging) also affects topology selection. This article focuses on the single-phase implementation of the OBC, as phase shedding [2] in 3-phase OBCs means that single-phase control strategies are also relevant for three-phase converters.
Onboard battery charger control strategy
Power factor correction
The power factor controller, shown in Figure 2, is a 2-stage cascaded controller based on the control from TN113 – Single-phase totem-pole PFC rectifier. The inner loop controls the grid current using a PR controller, and the outer loop controls the DC bus voltage using a PI controller.
Due to the nature of the single-phase grid connection, a 100 Hz (or twice the grid frequency) power ripple is inevitable, as no power from the grid can be transferred during the instances where the grid voltage is equal to zero. To ensure that the outer loop does not attempt to correct this ripple, its bandwidth must be reduced to below 100 Hz.
Feedforwarding a current equivalent to the charging power from the LLC ensures that the bus voltage does not drop during transients, improving controller performance.
Battery charger control
Compared to the rating of EV batteries, many onboard battery chargers charge the traction battery at a relatively low C-rate. Because of this, the charge current is limited either from the grid connection or the rating of the OBC itself. The charge current can therefore be set constant to the maximum rated current. At higher state-of-charges, the traditional technique is to charge using constant voltage to ensure that the battery is not overcharged [3].
It is noteworthy that research on batteries is constantly evolving, and the charging technique mentioned above is only one of many possible techniques that can be implemented [3].
Furthermore, due to the long charging duration for EV batteries, the dynamics of the current tracking are less relevant compared to the rejection of the 100Hz ripple on the DC bus. Therefore the control implemented in this section, shown in Figure 3, is an extension of the control implemented in TN126 – LLC resonant converter for battery charging applications. Along with the PI controller, a resonant controller is added in parallel to better reject the 100 Hz ripple.
The kr gain must be tuned conservatively to ensure stability as it is a linear controller acting on a non-linear plant (similar to the PI gains discussed in TN126). This is why the 100 Hz ripple cannot be completely eliminated by this control method.
Realization of an onboard battery charger using imperix products
System setup
The topology considered for the practical demonstration of the onboard battery charger, shown in Figure 4, is a totem-pole active rectifier in series with an LLC series resonant converter. The only non-standard component utilized in the commissioning of this system is the custom resonant tank for the LLC converter. Additional details about it can be found in TN127 – Tank circuit design for an LLC resonant converter. The system is assembled in a standard 19″ server cabinet and is shown in the figure below.
Standard component list
- 1x B-Box RCP, used as programmable controller
- 1x 2.2mH inductor, found in Passive Filters Box
- 1x AC grid panel 230 V
- 1x reversible DC power supply, used as a battery emulator at the output, with a configurable voltage
- 1x DIN 800 V voltage sensor, to measure the grid voltage
- 1x DIN 50 A current sensor, to measure the the output current
Due to the varying conditions that each module will be operating in, the optimal module for each part of the OBC, shown in Figure 6, is different:
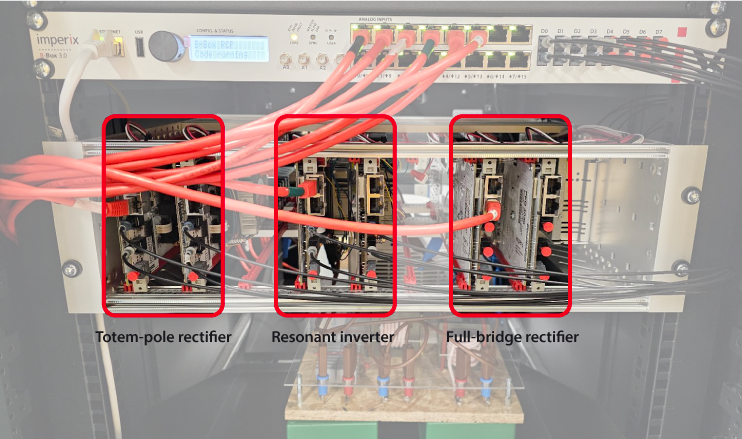
Control implementation in Simulink
The control strategy described in section 2.3 can easily be implemented onto the B-Box RCP using Simulink with the ACG SDK. The model shown in the figure below can be downloaded and run both offline and on the physical controller.
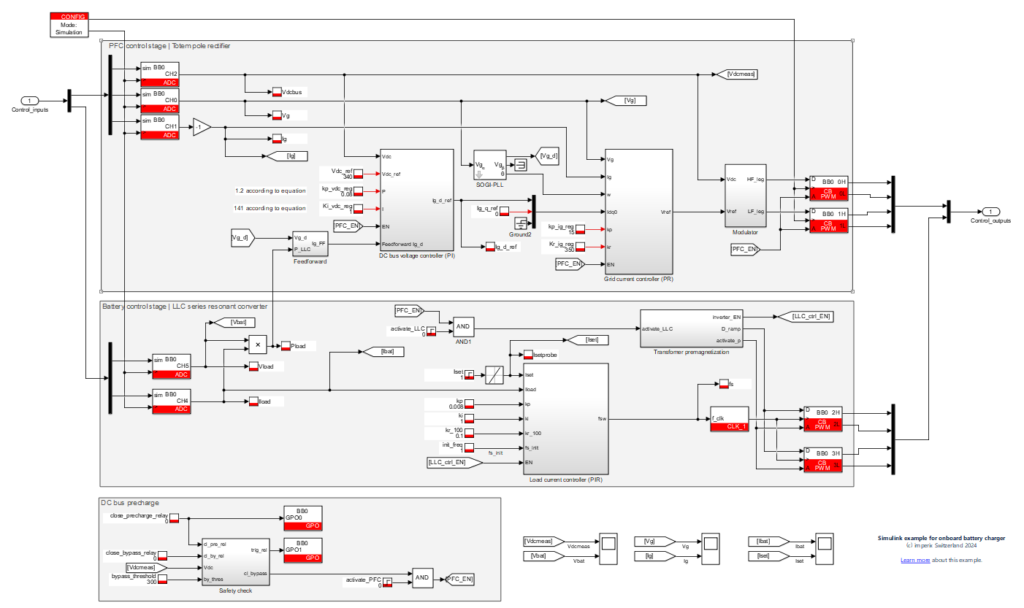
Onboard battery charger experimental results
The results in this section are limited to a specific battery voltage and are obtained by emulating the battery with the reversible DC power supply set to 400 V.
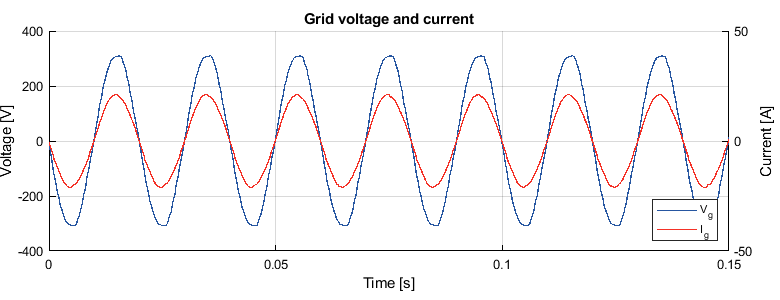
Figure 8 shows the grid voltage and current. The power factor of the onboard battery charger is 99.94% with 2% THD.
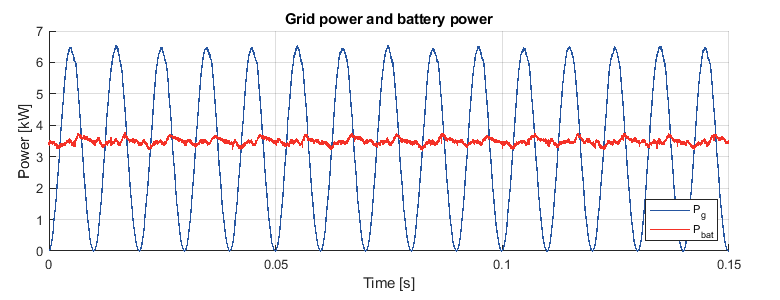
Power ripple from a single-phase system is inevitable and energy storage is required to mitigate its effects. Figure 9 demonstrates that despite the power ripple due to a single-phase connection to the grid, the energy stored in the DC bus allows for constant current charging of the battery.

Figure 10 illustrates the 100 Hz DC bus voltage ripple rejection of the LLC converter using the control strategy described in section 2.3.2. While the DC bus voltage ripple increases proportionally to the load current, the non-linear transfer function of the LLC stage results in the ripple rejection varying non-linearly with the load current.
When Iset is equal to 8.75 A, the voltage ripple is 17 Vpp, resulting in the voltage gain fluctuating from 1.15 to 1.21, and the current ripple is 1.25 A.
References
[1] A. Khaligh and M. D’Antonio, “Global Trends in High-Power On-Board Chargers for Electric Vehicles,” in IEEE Transactions on Vehicular Technology, April 2019
[2] C. Wang, M. Xu, F. C. Lee and Z. Luo, “Light load efficiency improvement for multi-channel PFC,” in Proc. of PESC, Rhodes, Greece, 2008
[3] W. Shen, T. Tu Vo and A. Kapoor, “Charging algorithms of lithium-ion batteries: An overview,” in Proc. of ICIEA, Singapore, 2012